Help Lightning Blog
Using Augmented Reality to Prevent Unplanned Downtime in Manufacturing
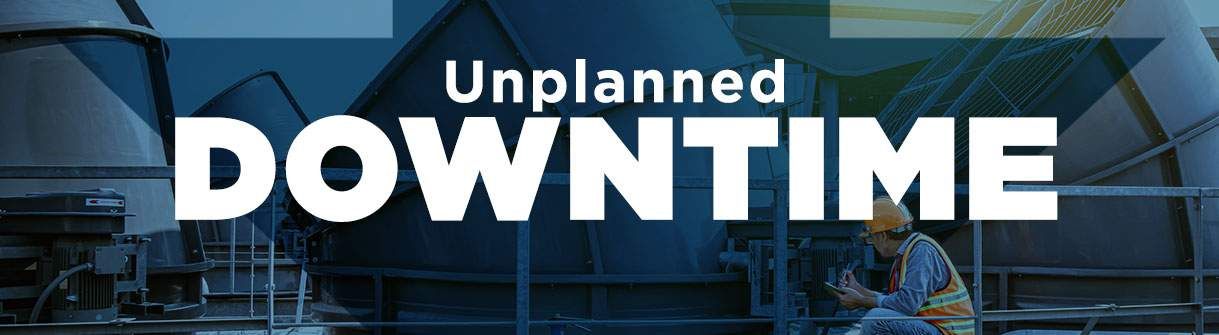
Unplanned downtime is a leading source of lost revenue and reduced productivity for many manufacturing companies – not to mention a major headache. However, while unplanned downtime was once accepted as ‘this is just how it goes,’ advances in technology are proving it can become a rare event. Many companies are even aiming for zero unplanned downtime as a key operational goal.
Together with Blumberg Advisory Group, we recently put together a comprehensive guide on reducing the cost of downtime: Remote Visual Assistance: The Optimal Last Mile Support Tool for Reducing the Cost of Downtime. In it, we explore the true costs of planned and unplanned downtime, how to calculate downtime costs, and we discuss impactful downtime scenarios many companies find themselves in. Additionally, we look at how companies can leverage Remote Visual Assistance (RVA) technology to optimize operations to reduce, and potentially eliminate, unplanned downtime.
This article explores how using RVA powered by augmented reality enables manufacturing companies to prevent unplanned downtime. Be sure to access Remote Visual Assistance: The Optimal Last Mile Support Tool for Reducing the Cost of Downtime for a comprehensive overview of this topic and more.
Is Zero Unplanned Downtime Possible in Manufacturing?
Reducing unplanned downtime is a top priority for most manufacturing companies. Attaining zero unplanned downtime requires a level of proactive maintenance and data-driven predictability. While it may not be possible to predict every possible issue that could lead to unplanned downtime, advances in technology greatly reduce many unknowns.
The Internet of Things (IoT) is often discussed as a solution, although we are not yet at a point with this technology where it’s easy to implement. In short, IoT requires a series of smart sensors designed for specific equipment, and has the capability to gather predictive data and detect when something is about to go wrong. It then ‘communicates’ with other parts of the system to either fix itself if possible, or alert a human who can manually fix the impending problem.
The necessity of installing sensors to detect and alert for potential forthcoming failures proves to be a barrier for many manufacturing companies. These companies are already busy and have established workflows — any solution to help reduce unplanned downtime requires reasonable ease of implementation. Consequently, zero unplanned downtime becomes more attainable with the right solution.
How Companies are Using Remote Visual Assistance to Prevent Unplanned Downtime
Remote visual assistance (RVA) is a technology that leverages augmented reality and enables users to merge video streams on any device. Both sides of the screen are able to engage as if they are side-by-side in the same space together. This includes reaching into each other’s screens to demonstrate how to engage with equipment, annotating screens, freezing frames, and incorporating tools into merged screen demonstrations. Onboarding is fairly simple, and engagement is tailored based on how the manufacturer wants and needs to use it.
Manufacturing companies using Help Lightning report reductions in unplanned downtime. RVA makes it possible for skilled technicians to be made available instantly onsite without having to account for travel time or onsite accessibility. With RVA, it’s easier for plant managers, foremen, and technicians to consistently review a range of operations to ensure optimal function. This includes consistent inspections of hardware and software, as well as performance reviews and training for equipment operators. Failures in these areas tend to be where most unplanned downtime occurs. Regular inspections and proactive engagement enable manufacturers to identify and preempt problems before they occur.
For example, run-to-failure can have negative consequences on the total machine, overall operations, and most importantly, worker safety. On the other side, time-based preventative maintenance can raise costs for replacement parts, increase the necessity of planned downtime, and create more overall disruption. RVA supports a balance between the two to help manufacturers minimize both planned and unplanned downtime in favor of proactive maintenance.
An additional problem with unplanned and planned downtime is when it’s extended due to lack of technician availability and malfunction during startup. RVA can be used to ensure technicians are easily available, and onsite technicians can receive expert oversight to ensure a smooth startup.
For more information on consequences and solutions for planned and unplanned downtime, be sure to check out our guide Remote Visual Assistance: The Optimal Last Mile Support Tool for Reducing the Cost of Downtime.
Get Help Lightning’s Guide on Leveraging RVA to Reduce the Cost of Downtime
Be sure to get our comprehensive guide to reducing the costs of downtime: Remote Visual Assistance: The Optimal Last Mile Support Tool for Reducing the Cost of Downtime. It discusses the types of downtime, goes into the specific consequences of downtime, provides information on calculating your company’s cost of downtime, and how to reduce – and even prevent – planned and unplanned downtime. This is a must-have guide for manufacturing, energy, and service companies aiming to optimize operations for profitability, productivity, and overall customer experience.