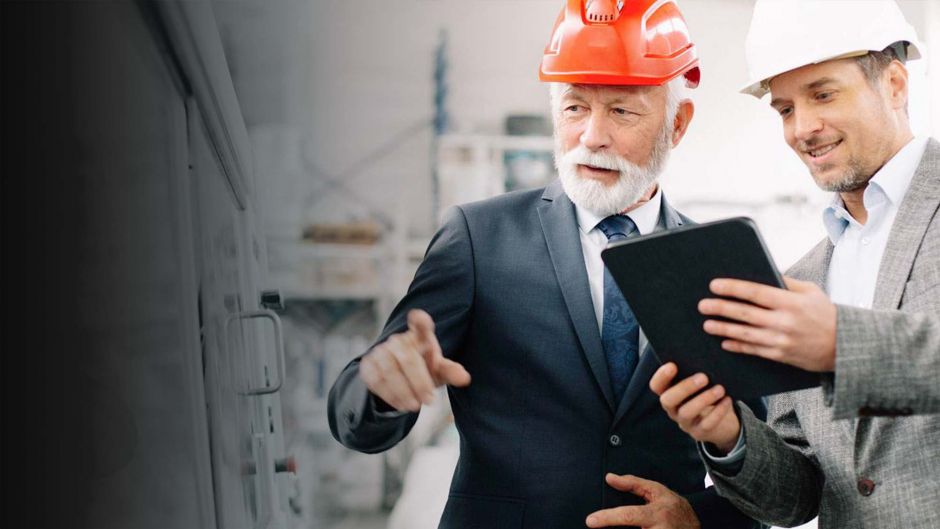
HELP LIGHTNING SOLUTIONS for MANUFACTURING
Improve Safety, Problem Resolution, and Operational Efficiency
HELP LIGHTNING SOLUTIONS for MANUFACTURING
Improve Safety, Problem Resolution, and Operational Efficiency
70000
Users
200
Companies
80
Countries
Improve Equipment Uptime
Reduce Resolution Time
Improve Customer Satisfaction
Explore the
Help Lightning Platform
Visual Remote Guidance Platform
for Enterprise Transformation
-
Hyper‑Quick Merged Reality
Unlock the power for extremely fast, accurate remote expert assistance with patented Merged Reality.
Merged Reality is a virtual, side-by-side video collaboration with blended “live” hand gestures, overlayed visual instruction, curated quick knowledge, alpha-channel-enabled visual aids, pre-selected troubleshooting, and merged demonstration using real tools and equipment. Merge content and real interactions with AR spatial understanding and annotations.
-
AI Speed-Assist
Help Lightning’s new AI capabilities offer a suite of innovative tools designed to enhance remote support and collaboration.
The platform features VoiceScript AI (real-time transcription and translation during calls), IntelliAssist AI (agent interaction with AI during calls for troubleshooting support and visual assets), ClearSight AI (visual analysis of screenshots and images to retrieve relevant model information for rapid knowledge access), SmartFolders AI and SmartTag AI (automated organization and asset tagging for easy retrieval), and GuidePoint AI (step-by-step procedural action generation from text-based content, notifying agents upon completion).
-
Curated Quick Knowledge
Share and manage smart, quick knowledge in visually guided procedures, chat, and merged reality fast help sessions.
Manufacturers and service organizations accelerate precise communication with curated model and serial number related images, videos, guides, PDFs, drawings, and models from enterprise content. Understand flows quickly for installation, troubleshooting, safety, sales and break/fix service in merged reality or chat sessions.
-
Auto-Guided Self-Help
Enriched standard operating procedures with video,
AR, and annotated pictures that can be authored by
any user enterprise-wide.Ensure compliance at each step. Eliminate delays and issues altogether with instant access to a context-aware, mixed reality remote expert at any step for inspection, validation, education, or problem resolution.
-
Industry 4.0 Spatial Computing
AR visualization helps you find assets easily. Quickly locate faulty equipment in a crowded, multi-asset environment by scanning the field with your mobile device or smart glasses.
Quick access to organizational knowledge from multiple sources — subject matter experts, guidance automation, knowledge bank, IoT real-time data and enterprise content — improves efficiency and minimizes downtime. Get real-time stats about the system’s components from your mobile device. View the big picture with unmatched spatial computing accuracy to find what you need to get the job done faster. You can even add merged-reality remote expert collaboration for speed to resolution and unmatched uptime.
-
AI‑Enabled Value Analytics
Sophisticated value analytics for you to understand your successes and where there are opportunities to improve. AI support for trend predictions and what-if analysis is included.
Drill down through interactive visual scorecards and metric measurements by region, division, product-line, equipment model, customer, incident type, even user groupings and skills, to understand what is working well and where you need to improve.
Manufacturing Use Cases
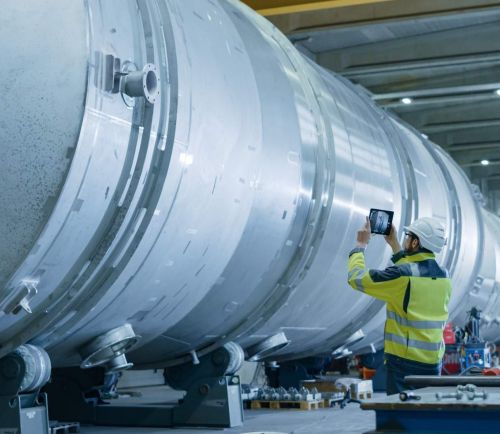
INTERNAL
Factory Equipment Installation
Remote virtual assistance software enables engineers to use their expertise virtually guide customers through the installation process. They can provide accurate directions, and call in additional experts as needed.
Support is available in real time, helping to ensure equipment is properly installed. This is true even if the person doing the hands-on work is not familiar with the installation process.
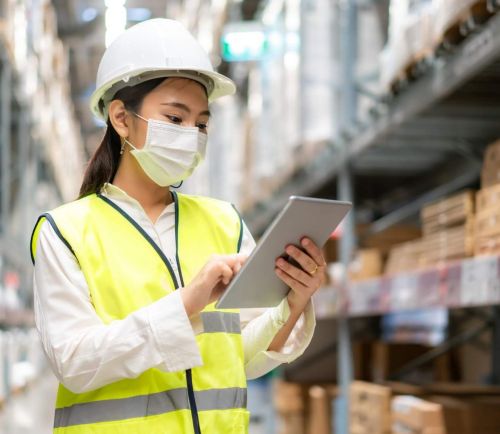
INTERNAL
Safety Audits
Timely audits are essential for workplace safety. They are also required to maintain compliance with laws and regulations. Additionally, a complete audit is often needed to obtain permits, and is sometimes required to contract jobs.
Remote visual assistance software allows you to conduct thorough safety audits. You can easily maintain standards for machinery, job sites, technician safety compliance and much more. All at a fraction of the time and cost of in-person audits.
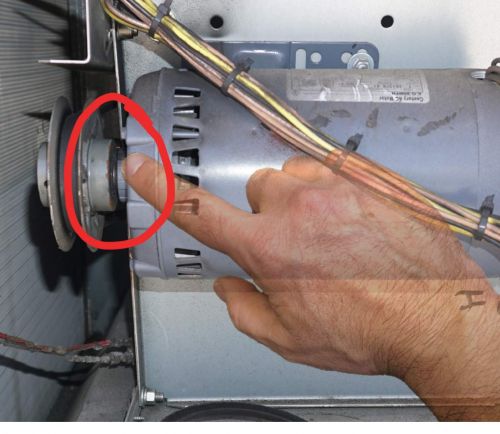
EXTERNAL
Factory Acceptance Testing (FAT)
Additionally, time and manual labor required for effective FATs can be costly to the manufacturer. Especially if they do not meet customer criteria and require additional time and manual labor.
An ability to conduct factory acceptance tests with the help of remote visual assistance software benefits both the manufacturer and customer.
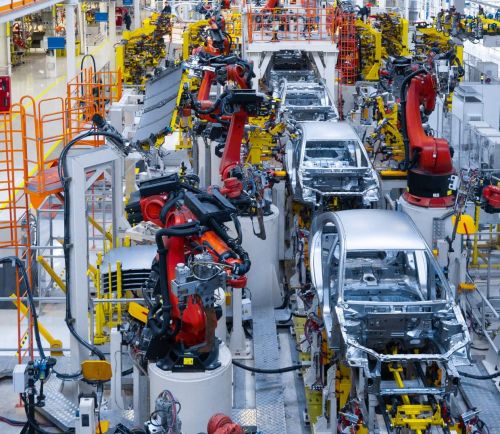
INTERNAL
Production Line Optimization
Remote virtual assistance software offers the ability for research and development engineers to support factory engineers. And they can do this in real time, from any location.
They can review production line first batches, and help fine tune for full production. The line can be effectively audited to ensure optimal functionality for the given operation.
CASE STUDY
What Our
Customers Are Saying

“Pretty much every use is a ‘success story’ …customers appreciate the technology, and it works every time.”
Explore the
Help Lightning Platform
ADDITIONAL MANUFACTURING RESOURCES
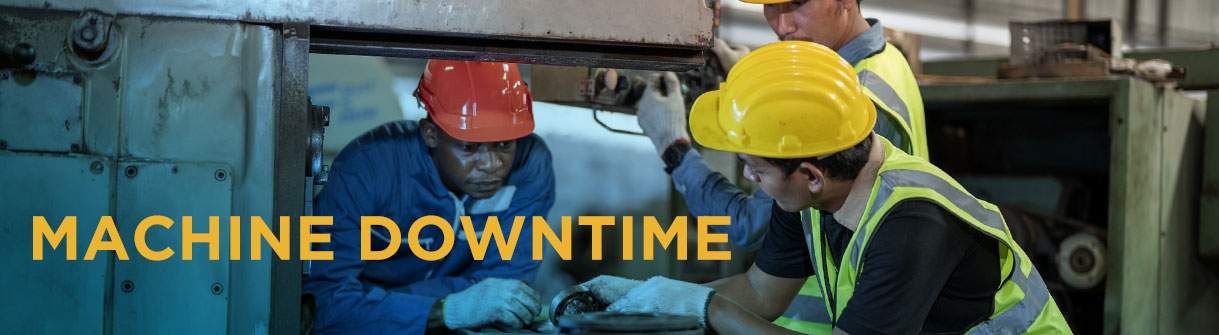
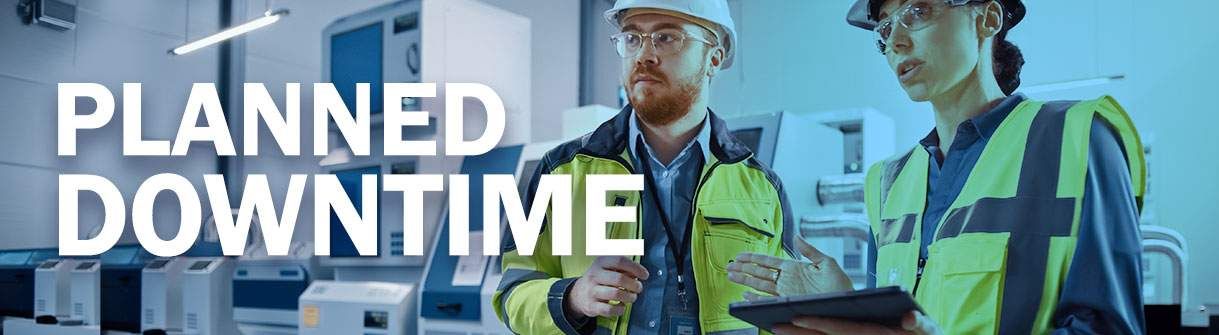
Optimize Planned Downtime Using Remote Visual Assistance
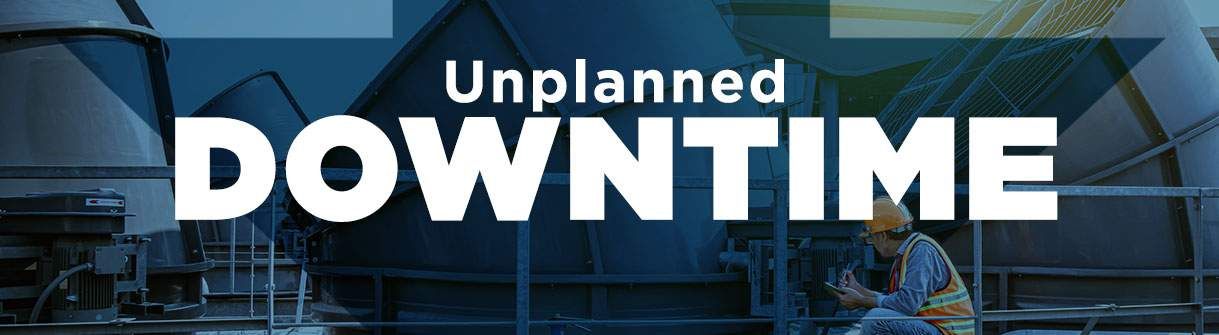